We were approached by an existing customer to design a manufacturing process for a formed bar retainer that holds three ball bearings of two different sizes for use in passenger car seat tracks. We had produced progressive dies for two similar retainers for this customer but this version presented a number of unique challenges.
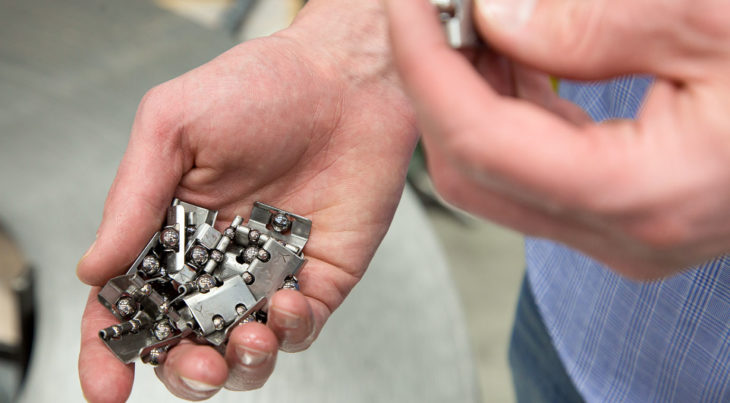
CHALLENGE
- Insertion and retention of two different size ball bearings
- Consistent, free movement of the balls within the part
- Inspection to determine the presence of three ball bearings in each part
- Mandated 100% product perfection
- Manufacture of two identical parts simultaneously
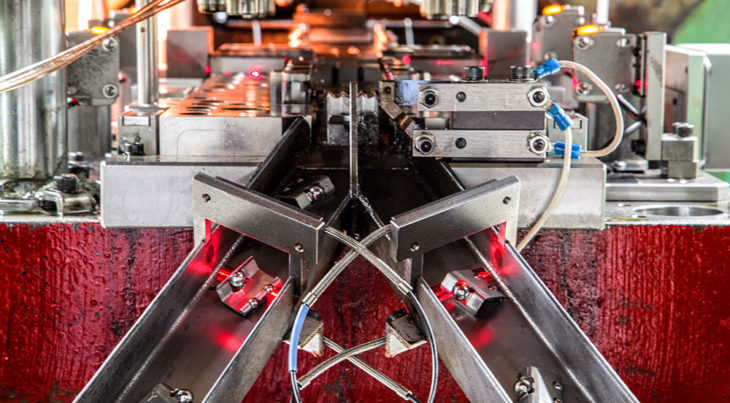
DESIGN
Our first design incorporated the method of ball bearing insertion and retention that we had used in the first two projects completed for this customer. However, our initial Design Review Team (DRT) meeting determined that neither of these methods would satisfactorily meet the customer’s current requirements.
Our redesign process revealed a new approach that presses the blanked and curled part over the small ball bearings at one station and over the large bearing, from below, at another station. The part form is finalized following those operations and results in bearings that are secured within the part and are able to freely rotate without binding. The design feeds six ball bearings per operation from two sources to two parts at the same time.
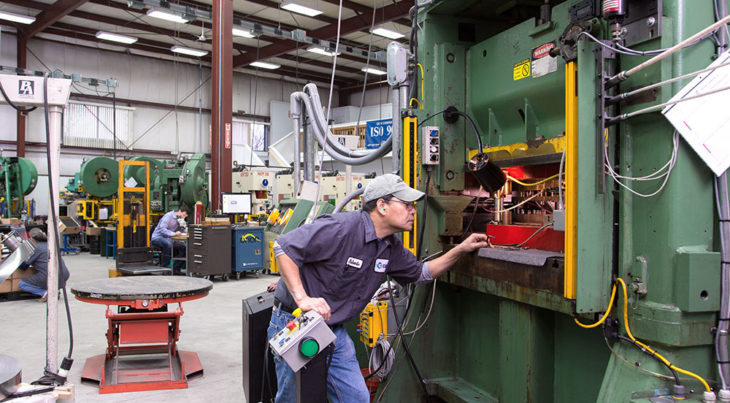
RESULTS
The progressive die includes an in-tool inspection method that senses the bearing count in each part before it leaves the press, allowing us to confidently ship completed, zero-defect parts directly to the customer’s assembly area.
The project was completed to customer’s specifications and stayed within their budget. Orders for this part have increased each year from an initial order of 8 million/year to a current quantity of 35 million/year, utilizing a second tool, also designed and built at CEI.
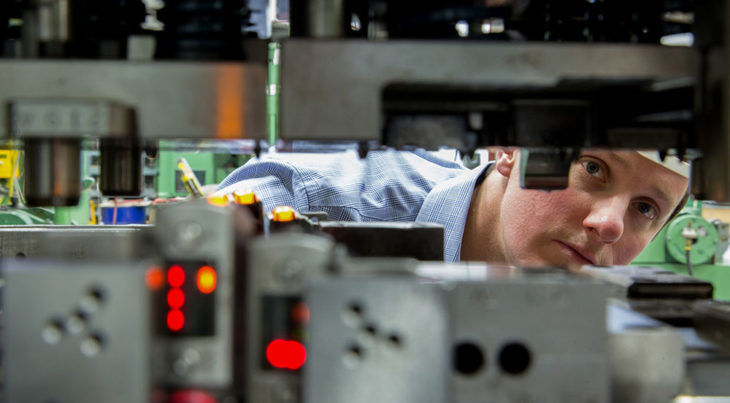