One of the world’s largest dental supply chains approached us to help develop a new product line of abrasive disks for use in the tooth repair process. They had developed a unique abrasive and applied it to Mylar sheets in coil form, and they needed four varieties of abrasive disks that would be affixed to a dentist’s drill. In addition, in order to break into this new market, they needed to offer their customers a significant cost savings compared to the incumbent disk brand.
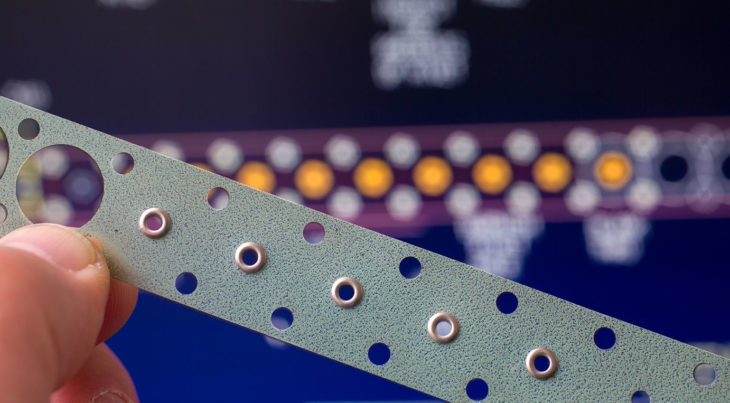
CHALLENGE
During our analysis of the customer’s part print we identified the following technical challenges:
- Orientation of rivet
- Correct formation of rivet
- Feeding and positioning of rivet and disk in a progressive die at reasonable speed
- Cutting of an abrasive material without wearing out or dulling the cutting members prematurely
- The ability to cut two different thicknesses of material
- The ability to cut two different size disks
- The ability to cut and maintain tool with two different grits of abrasive
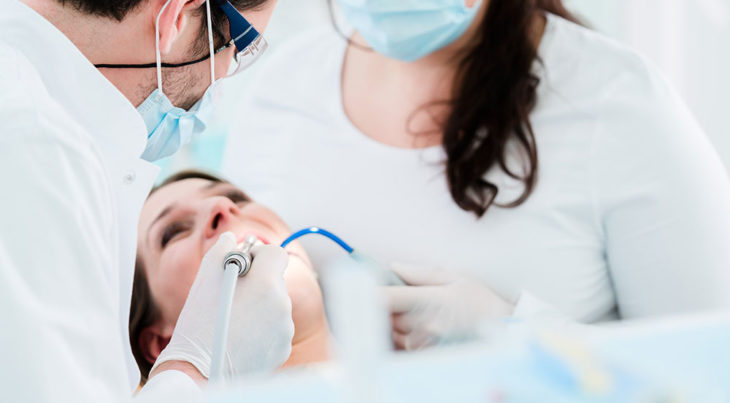
DESIGN
The original rivets varied to the extent that consistent manufacture of disks was impossible. We developed the necessary dimensions and tolerances to achieve the goal of dimensional stability and consistency from part to part. Through an extensive research and development process we developed the optimum geometric shapes for the punches and dies that allowed for continuous, successful forming of the rivet.
In developing these punches and dies, four different grades of tool steel were tried, in conjunction with two different coatings. Adding to the challenge of correct formation of the rivet was the requirement to have two different thicknesses of disks along with two different grits. Each of the four disk combinations required independent design, manufacture, and debugging of a forming punch and die.
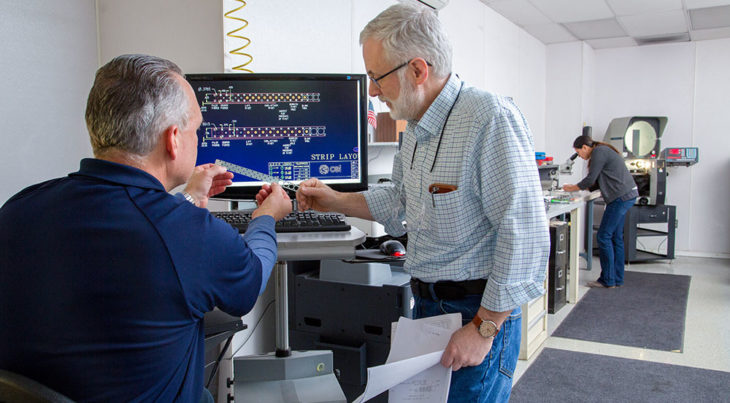
RESULTS
During the project we:
- Designed and built a proprietary and unique system for delivering a small custom manufactured rivet into a progressive die
- Designed and built an orientation system to properly align the rivets with the abrasive disk material, which has been partially manufactured utilizing progressive die technology
- Developed and built a unique formation process that properly retains abrasive material to the rivet in a precise and consistent orientation.
- Utilized unique materials to develop a precise cutting tool that resists the wear that would normally be caused by cutting abrasive material.
- Designed and built a progressive tool capable of producing disks with different thicknesses, grit size, and diameters.
The resulting automated, maintainable process delivers four consistently accurate product lines that provide our customer with a cost and quality advantage compared to their competitors.
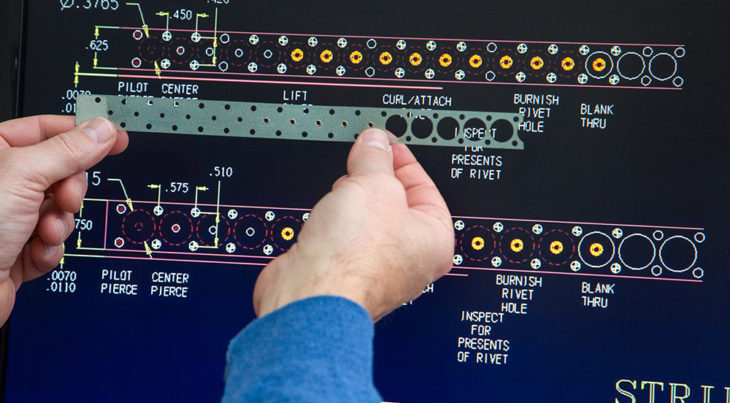