A supplier in the medical industry contacted us regarding production of an EMI Shield. They were interested in reducing their costs while retaining the quality needed to maintain their market position as a reliable provider. This required a long term commitment from the customer, which in turn allowed CEI to develop and build the automated tooling which would allow the parts to be fabricated by only one operator.
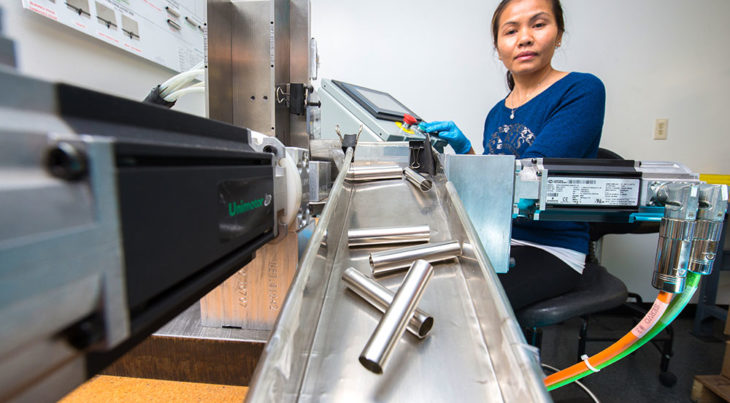
Challenge
As with all passive EMI shields, a primary challenge is working with Mu-Metal. It is extremely thin, easily damaged, and requires extraordinary handling precautions.
The first stage of this project was to devise a manufacturing process that would produce a flat blank with folds across both ends. Next, and even more challenging, we needed to roll the material to produce a loose tube with an overlapping of material to be welded later in the process.
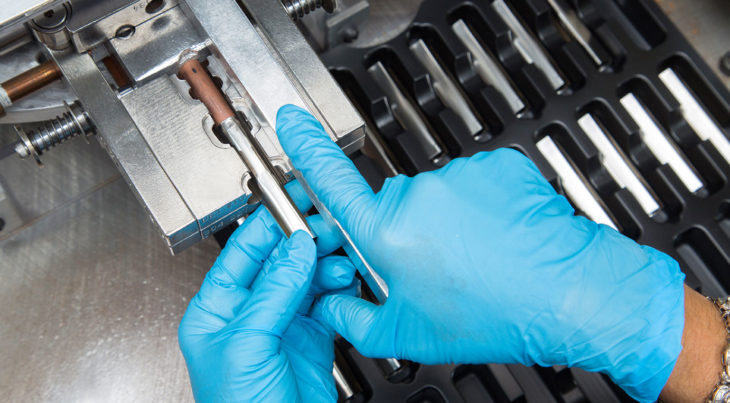
Design
Our tooling design included a shaped mandrel inserted through the tube then placed into a holder. A blade form punch was the placed on top of the tube then squeezed to shape the metal.
In order to produce three resistance spot welds along the overlapped section of the tube, our team developed tooling to perform the delicate process of holding the loose tube to a fixed diameter while the dart was welded. A final heat treat process was required to reset the magnetic permeability of the material, which was lost during the forming and welding of the part.
To prevent damage during shipping, a plastic tray was designed and produced to cradle each part individually.
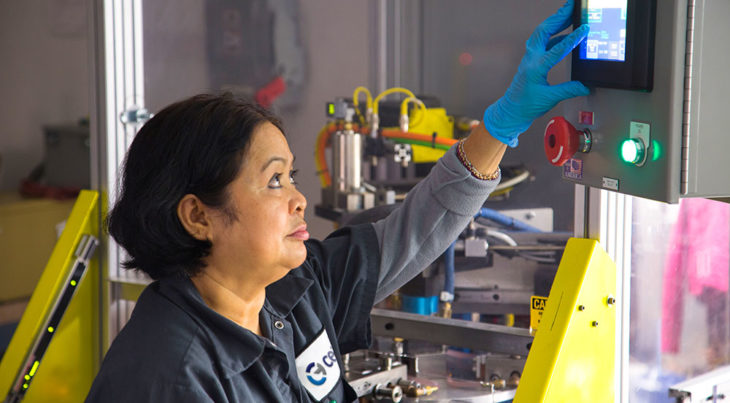
Results
Following the successful production of the 500 required prototype parts:
- A progressive die was designed and built to produce a coupon that included folds on two sides of the coupon.
- A CNC machine was designed and built into which a stack of coupons is loaded. The machine would activate servo motors to feed the coupons into the open rollers, air cylinders would close the roller onto the coupon another servo motor would rotate the coupon through the three rollers producing a loose tube.
- A tabletop forming machine was designed and built by CEI. It was designed with a complete air logic system to ensure consistency.
- A welding machine was built. Each weld was monitored for the required amperage to create a perfect weld.
As with much of the work our customers rely on us to complete, this project required the cooperation, knowledge and expertise of several different departments in the shop and blended a variety of talents to build the necessary dies, fixtures, and tooling.
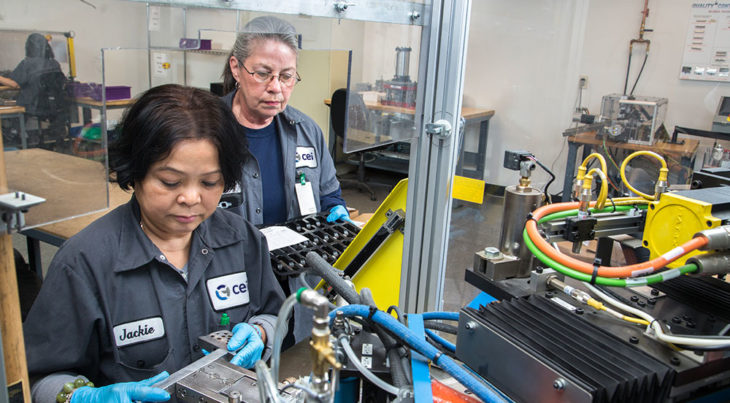