A leading supplier of optical fiber tools contacted us to manufacture blades for a new hand-held fiber optic cable stripper. Using the tools available at the time, installers could easily nick the glass fiber while removing the outer jacket. This new design eliminated nicking which shortened installation time and reduced material waste.
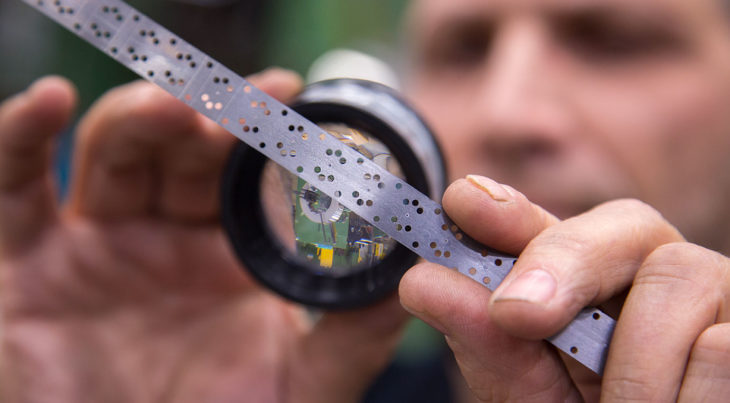
CHALLENGE
We were asked to design, build and run an interchangeable progressive die to produce a coil of fiber optic stripping blade product in 18 different configurations. The customer’s part print for the project, which was considered unchangeable, had dimensions with tolerances that dictated how the progressive die must be designed and built in order to produce a part with the precision and accuracy they required.
DESIGN
Every project at CEI begins with a review of the customer’s purchase order and part print. The initial concept layout for the progressive die revealed that there was an immediate requirement for the customer to make a change to their part print. Working with us on this change, they added holes to the part print per our suggestions.
The strip layout is the first step in the progressive die design process. CEI utilizes a Design Review Team (DRT), which represents the departments that will ultimately build, run and inspect the progressive die and product, to review this stage of the process.
Part features include:
• Center hole with chamfer depth at 80% of material thickness
• Two vertical score-grooves
• One horizontal score-groove
• Six (diameter .060”) holes
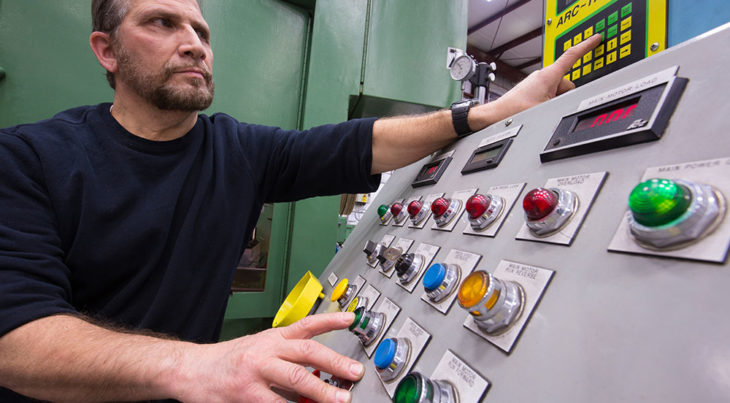
RESULTS
The part is a Reel to Reel product, employing a production method in which the coil is re-rolled after it is fed through the progressive die. The coil is then sent to a facility where it is heat treated to hardness of RC 58-60. Our customer then takes delivery of the coils, cuts them into segments, and assembles the Fiber Optic Stripping Tool.
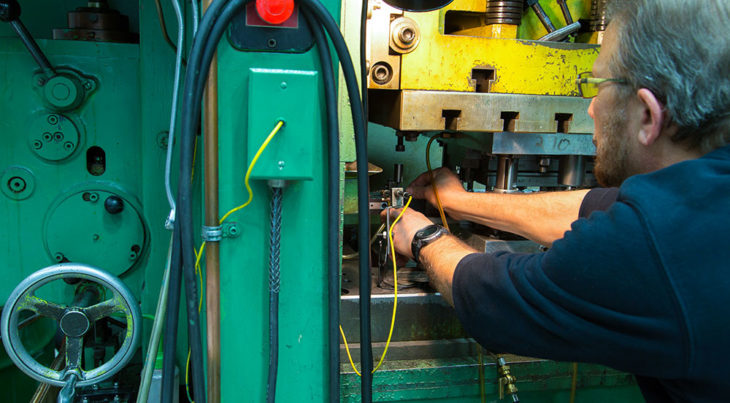